Het is één van de spannendste innovaties van dit moment: 3D-betonprinten. Eén van de vaandeldragers van 3D-printen met betonmortel is Saint-Gobain Weber Beamix, die je als vakman kent van de gele zakken mortel in het Bouwmaat schap. De fabrikant heeft de ambitie om door innovatie en experimenten de inzet van 3D-betonprinten in een stroomversnelling te brengen. Begin dit jaar werd hierin een nieuwe stap gezet door samen met BAM Infra Europa’s eerste industriële productielocatie voor 3D-betonprinten te openen. Bouwmaat ging naar Eindhoven en sprak daar in het hoofdkantoor met Bas Huysmans, CEO van Saint-Gobain Weber Benelux. Uiteraard konden we het ook niet laten om even bij de 3D-printer zelf te kijken.
De noodzaak van anders bouwen
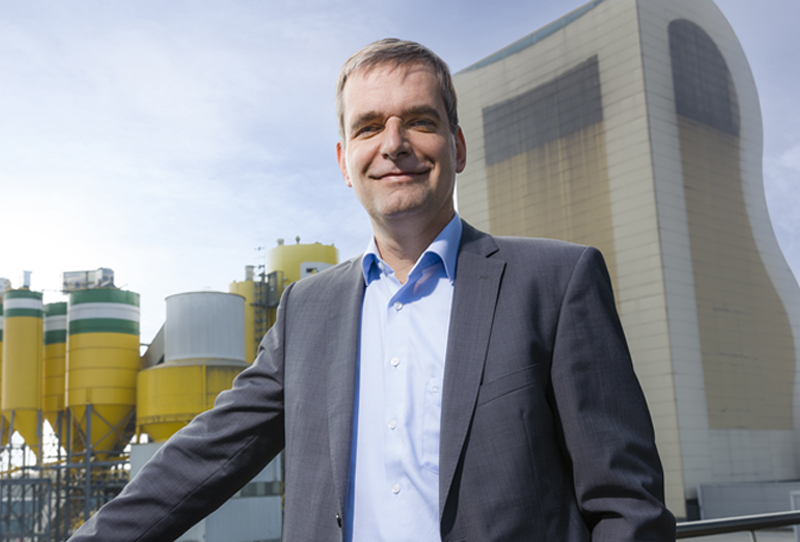
Het bedrijf heeft een lange geschiedenis met 3D-betonprinten. Na een aantal jaar experimenteren werd aan de hand van een handgestuurde 3D-printer in 2005 al een 3D-geprinte muur gemaakt. Het 3D-printen van beton in Nederland was hiermee in feite geboren. Door de beperkte vraag uit de markt bleef de techniek wel op een laag pitje. In 2015 raakte 3D-betonprinten in de volgende versnelling door het onderzoeksprogramma 3D Concrete Printing (3DCP) van de Technische Universiteit Eindhoven. De universiteit werkt hierin samen met een groep aannemers, bouwmaterialenfabrikanten en ingenieursbureaus.
Het bedrijf heeft een lange geschiedenis met 3D-betonprinten. Na een aantal jaar experimenteren werd aan de hand van een handgestuurde 3D-printer in 2005 al een 3D-geprinte muur gemaakt. Het 3D-printen van beton in Nederland was hiermee in feite geboren. Door de beperkte vraag uit de markt bleef de techniek wel op een laag pitje. In 2015 raakte 3D-betonprinten in de volgende versnelling door het onderzoeksprogramma 3D Concrete Printing (3DCP) van de Technische Universiteit Eindhoven. De universiteit werkt hierin samen met een groep aannemers, bouwmaterialenfabrikanten en ingenieursbureaus.
Saint-Gobain Weber Beamix kon hierbij niet ontbreken. Bas legt uit waarom het zo belangrijk is dat de techniek nu echt een vlucht gaat nemen: “We zullen met z’n allen op een andere manier moeten gaan bouwen. Iedere dag hoor en lees je in het nieuws over het gebrek aan bouwmaterialen en gebrek aan personeel. We lopen langzamerhand tegen de grenzen aan van wat fysiek mogelijk is. Eén van de oplossingen is automatisering. Het printen van gebouwde objecten is een hele mooie vorm van automatisering van het bouwproces en daar dragen wij graag ons steentje aan bij.”
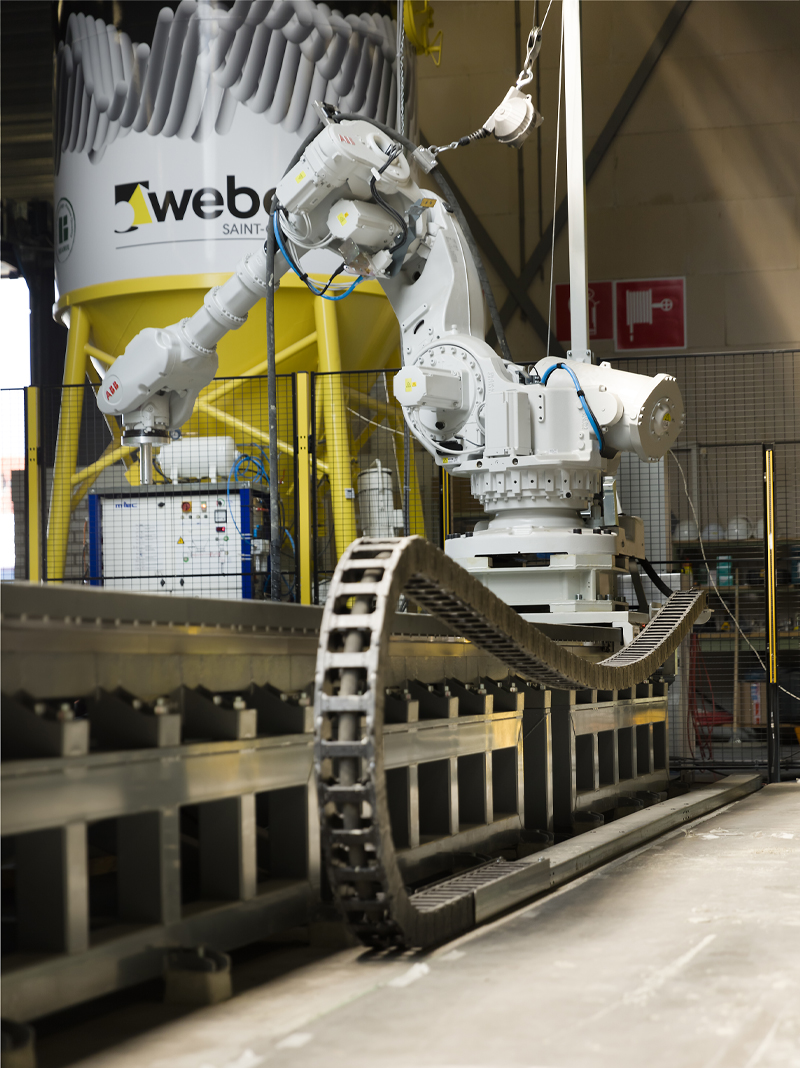
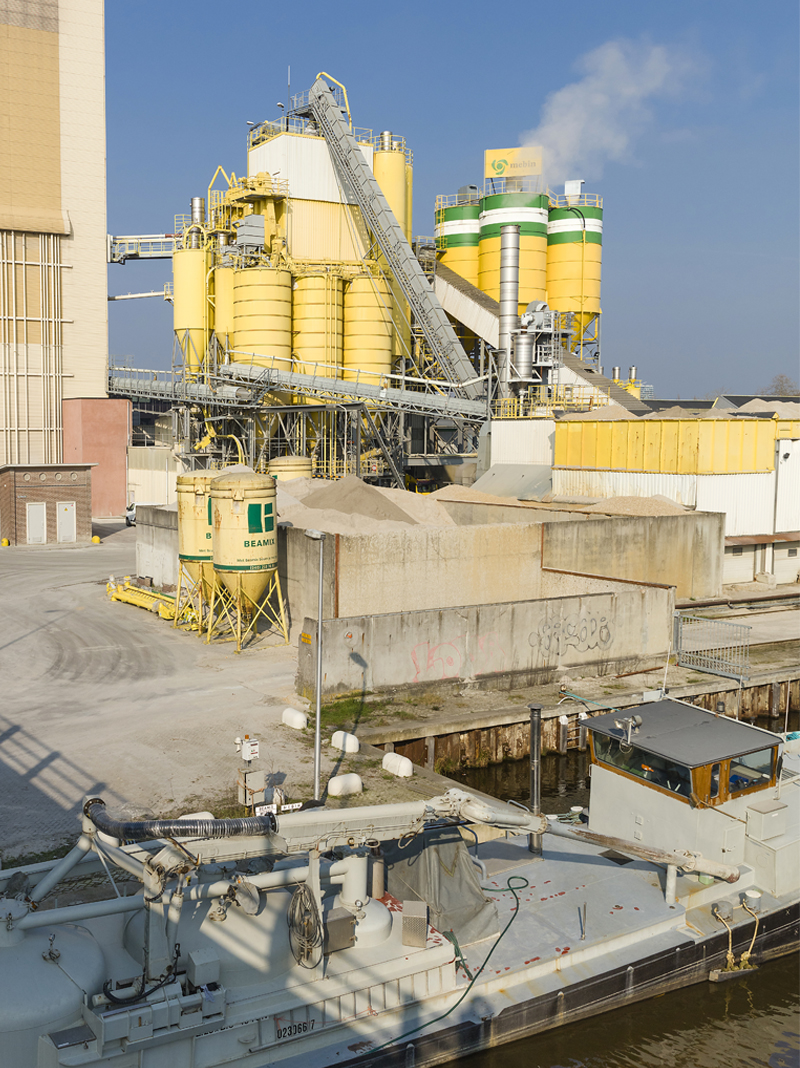
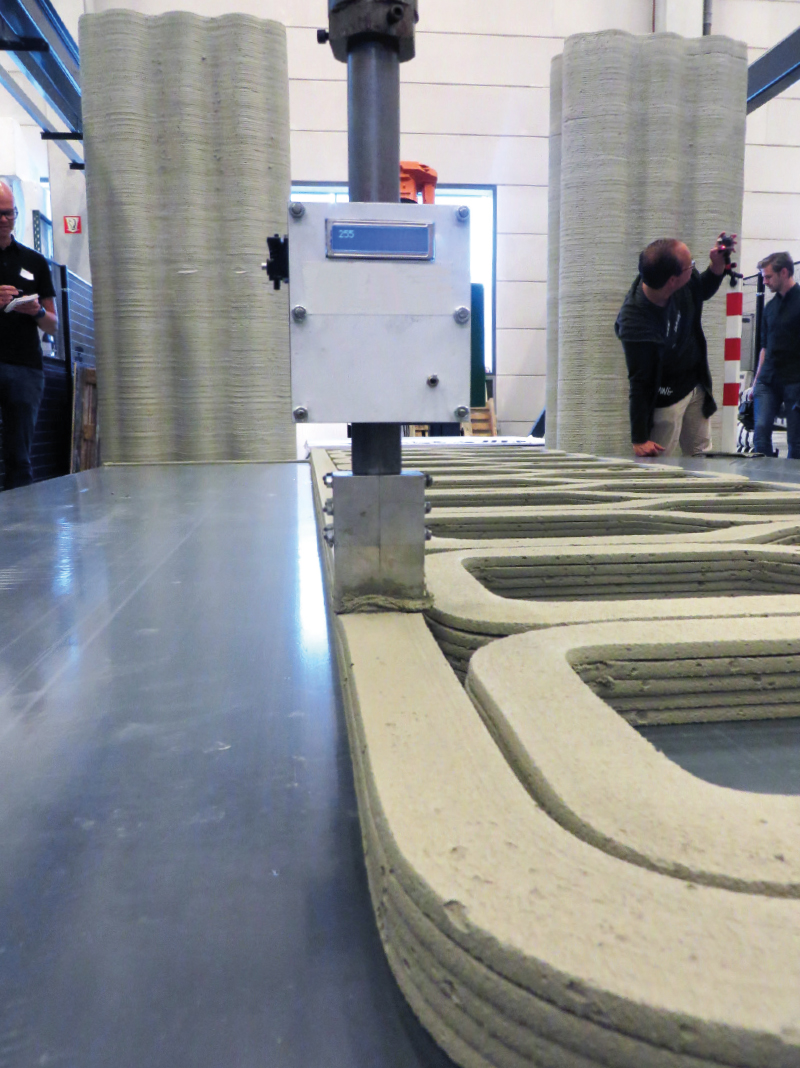
Wereldprimeurs in Nederland
De experimenteerdrang van SaintGobain Weber Beamix levert unieke projecten op. Zo werd eind 2017 in het dorpje Gemert de eerste 3D-geprinte fietsbrug ter wereld in gebruik genomen. Een project waarbij BAM Infra ook nauw betrokken was en een mooi voorbeeld van 3D-betonprinten in de praktijk. Het verdiende een vervolg.
Deze volgende stap was de eerste commerciële industriële productielocatie voor het 3D-printen van betonnen elementen, vlakbij het hoofdkantoor van Saint-Gobain Weber Beamix. In de printrij staan onder andere een viertal bruggen in samenwerking met de provincie Noord-Holland, een Nijmeegse brug in opdracht van Rijkswaterstaat en natuurlijk de huizen voor het Project Milestone.
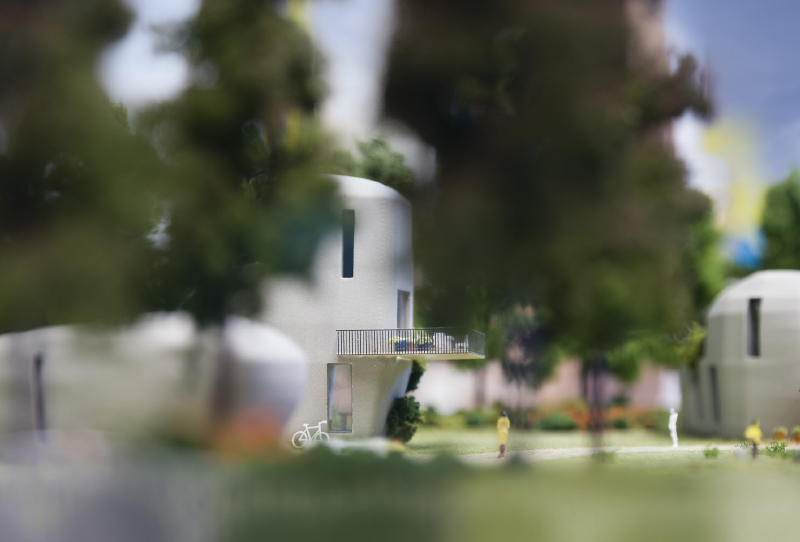
Project Milestone
Samen met de gemeente Eindhoven, TU Eindhoven, Van Wijnen, Vesteda, en Witteveen+Bos gaat Saint-Gobain Weber Beamix in de Eindhovense nieuwbouwwijk Meerhoven vijf bewoonbare woningen van 3D-geprint beton realiseren. De huizen worden na elkaar neergezet. De techniek wordt ondertussen verder uitgewerkt, zodat er per huis steeds meer mogelijk zal zijn.
Dit is nog maar het begin
Praktijkvoorbeelden genoeg dus, al is dit alles volgens Bas nog maar het begin. “We gaan de komende jaren nog heel veel ontwikkelingen zien rondom 3D-betonprinten. We zijn net begonnen. Er is geïnvesteerd in een installatie om uiteindelijk van de studieomgeving op te schalen naar de productiewereld. Dan hangt er meteen een kosten/opbrengsten plaatje aan, dat dwingt ons om daadwerkelijk projecten te realiseren. Die projecten hebben we nodig om ervaring op te doen.”
We weten al heel veel en we kunnen ook al enorm veel. De brug in Gemert is daar een mooi voorbeeld van, de woningen die we gaan printen in Eindhoven ook. We realiseren ons wel dat we nog heel veel moeten leren. En learning by doing is een term die hier perfect op z’n plek is. We zullen nog fouten maken, we zullen nog tegen dingen aanlopen waar we tot vandaag nog nooit aan gedacht hebben. Ik ben er echter van overtuigd dat als we de middelen en motivatie hebben, en de projecten waar we mee aan de slag kunnen, we die leerschool kunnen doorlopen en dat we alleen maar succesvoller zullen worden in 3D-printen.”
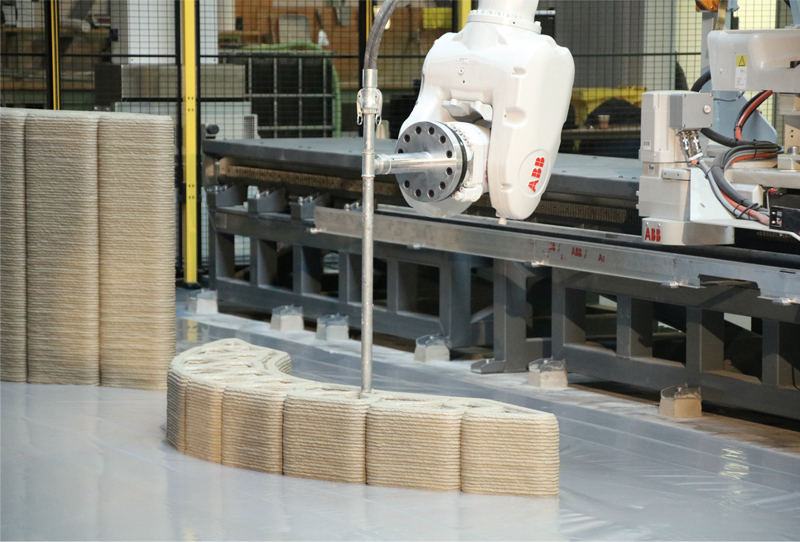
3D-betonprinten: de belangrijkste voordelen
De bouwsector kan volgens Bas niet meer om 3D-betonprinten en de beoogde voordelen heen. “Een belangrijk voordeel dat 3D-printen gaat bieden is vormvrijheid. Alles wat je bedenkt, kun je straks ook daadwerkelijk realiseren. Je hebt bijvoorbeeld niet meer te maken met bekistingsconstructies. Een ander belangrijk voordeel is dat je minder materiaal nodig hebt. Prefab betonelementen zijn massief gevuld. Die massiviteit heb je echter niet nodig. Door 3D-printen kunnen we holle constructies maken. Deze materiaalbesparing is goed, want we beginnen ons steeds meer zorgen te maken over materiaalgebrek. Maar minder materiaal betekent ook minder cement, minder CO2-belasting. Daarmee is 3D-betonprinten ook nog eens beter voor ons milieu.”
3D-betonprinten in het kort
- Geen beperkingen m.b.t. vorm
- Geen bekisting nodig
- Minder materiaal nodig
- Beter voor het milieu
EUROPA’S EERSTE INDUSTRIËLE PRODUCTLOCATIE VOOR 3D-BETONPRINTEN
Op een steenworp afstand van het hoofdkantoor van Saint-Gobain Weber Beamix vinden we de eerste industriële productielocatie voor 3D-betonprinten van Europa. Een vast team is hier de hele dag in touw met experimen- teren en het optimaliseren van het 3D-betonprintproces. Pronkstuk van de hal is natuurlijk de 3D-printrobot zelf.
De robot zorgt ervoor dat de printkop de mortel op de juiste plaats neerlegt. In die zin is de robot zelf dan ook niet heel bijzonder want in de automotive industrie wordt volop gebruik gemaakt van deze robots voor lassen en spuitwerk. De robot in de printshop is dan ook afkomstig van ABB dat als bedrijf heel veel ervaring heeft met deze toepassingen. Het bijzondere zit hem in de mortel en de printkop. Er kan zelfs ook staaldraad meelopen, waardoor elke betonlaag kan worden voorzien van de benodigde bewapening.
Ik vind dit artikel: